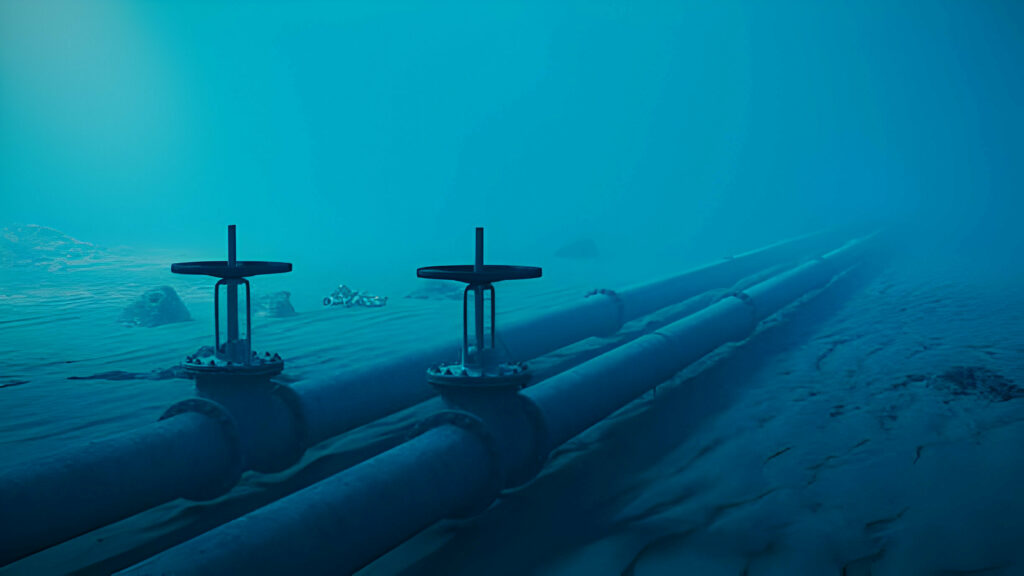
Underwater welding is one of the most specialized and demanding fields in the construction and repair industries, requiring professionals to perform welding operations while submerged in water, typically at great depths. This unique practice is essential for building, maintaining, and repairing structures like oil rigs, bridges, ships, dams, and underwater pipelines. The complexity and risks involved in underwater welding make it a highly specialized skill, demanding an in-depth understanding of welding techniques, the environmental challenges of working underwater, and, most importantly, stringent safety protocols.
This article delves into the techniques, challenges, and essential safety measures for underwater welding, exploring the innovations and strategies that help underwater welders perform their tasks efficiently and safely.
1. The Two Main Types of Underwater Welding: Wet vs. Dry Welding
Underwater welding is divided into two primary types: wet welding and dry welding. Both types have their distinct methods, uses, and considerations.
Wet Welding
Wet welding is the most common type of underwater welding and involves the welder performing the welding operation directly in the water. It requires specialized equipment to provide a stable arc and control the weld puddle in the harsh underwater environment. In wet welding, the welder typically uses a specialized electrode that is coated to withstand the challenges of working in the water, such as the loss of heat and electrical resistance caused by the surrounding liquid.
Advantages of Wet Welding:
- Cost-effective: Wet welding doesn’t require complex equipment or pressurized chambers, making it a less expensive option compared to dry welding.
- Quick and direct access: Wet welding is ideal for repairing underwater structures that are already submerged, such as pipelines, ships, and other marine structures.
Challenges of Wet Welding:
- Visibility and precision: The ability to see clearly underwater can be severely limited by the depth, water clarity, and the use of diving gear. This makes the welding process more difficult.
- Heat dissipation: Water absorbs heat quickly, which can lead to uneven cooling and weak welds.
- Electrical hazards: Wet welding involves working with electrical equipment in water, posing a risk of electrical shock, which can be fatal.
Dry Welding
Dry welding, on the other hand, is used when the work environment is enclosed in a dry, pressurized chamber, often referred to as a habitat. The welder enters this habitat, which is connected to the underwater structure, and performs welding in a controlled, dry environment.
Advantages of Dry Welding:
- Better control and precision: The welder works in a dry environment, allowing for more precise welding with conventional welding techniques.
- Improved weld quality: Dry welding allows for better control over heat and cooling, producing higher-quality welds.
Challenges of Dry Welding:
- Costly and complex setup: Dry welding requires a pressurized habitat, which can be expensive to set up and maintain. This makes it more suitable for larger projects rather than small, routine repairs.
- Limited access: The welder must enter the habitat, which may limit access to certain areas of the structure being welded.
2. Common Challenges in Underwater Welding
Underwater welding comes with a unique set of challenges due to the inherent nature of working in a submerged environment. Some of the most common challenges include:
Water Pressure
The deeper the welder dives, the higher the water pressure becomes, which can impact the welding process. The increased pressure can affect the flow of gases, cooling rates, and the integrity of the weld. High pressure can also lead to the expansion of gases, causing bubbles in the weld pool, which weakens the final weld.
Corrosive Environment
Saltwater is highly corrosive and can quickly degrade metal structures, including the equipment used by welders. This means that welders must work with materials that can resist corrosion and use tools and equipment that are specifically designed for use in marine environments.
Poor Visibility
Working underwater means that visibility is often poor due to limited light, murky water, and the use of diving gear. Welders have to rely on their experience and specialized equipment, such as underwater cameras or lights, to help them navigate and complete the welding job with precision.
Strong Currents
Strong ocean currents can make it difficult to maintain a stable position while welding underwater. Welders may need to use anchors, diving weights, or special rigs to hold themselves in place and reduce the impact of the current on their work.
Limited Work Time
Underwater welders work in a challenging environment, and there is often a limited window of time in which they can perform their tasks due to the limitations of their diving equipment, air supply, and physical fatigue. This makes it crucial for underwater welders to work efficiently while ensuring that the job is done to the highest standards.
3. Safety Measures in Underwater Welding
Safety is paramount when working in such a hazardous environment. Underwater welding is an inherently risky profession, and proper safety protocols must be followed to reduce the risk of accidents and ensure the welder’s safety and well-being.
Personal Protective Equipment (PPE)
Underwater welders must use specialized PPE to protect themselves from the dangers of working in an aquatic environment. The essential safety gear includes:
- Diving suit and helmet: To provide warmth and protection from the cold temperatures and protect the welder from debris or direct exposure to seawater.
- Welding gloves: These provide protection from the electrical risks and physical hazards associated with welding.
- Communication devices: Welders must maintain communication with surface personnel to ensure safety throughout the operation.
- Personal flotation devices (PFD): Welders must wear PFDs in case of emergencies, ensuring they can safely float to the surface if necessary.
Electrical Safety
Because underwater welding involves electricity in a conductive environment, strict measures are taken to avoid electrical shocks. This includes:
- Insulating welding equipment: Ensuring that the equipment is properly insulated to prevent leakage of current into the water.
- Grounding the system: Properly grounding all electrical equipment to prevent accidental shocks.
- Regular equipment checks: Inspecting equipment thoroughly before and during the job to ensure it is in proper working condition.
Decompression Procedures
As with all diving activities, underwater welding involves the risk of decompression sickness (the bends), which occurs when a diver ascends too quickly from deep water, causing nitrogen bubbles to form in the bloodstream. To avoid this, welders must follow decompression procedures that involve staged ascent and a period of time spent at various depths to allow the body to safely expel the nitrogen.
Training and Experience
Underwater welding requires extensive training and experience in both welding techniques and diving. Welders need to be certified as commercial divers in addition to being skilled welders. They must understand both the science of welding and the nuances of underwater environments to perform tasks safely and effectively.
4. The Future of Underwater Welding
The field of underwater welding continues to evolve with advancements in technology, equipment, and training. Innovations such as robotic welding systems and automated welding techniques are beginning to assist underwater welders, particularly for jobs at great depths or in highly dangerous conditions. Additionally, improved remote monitoring systems and drones are enabling better assessment of underwater welding projects, allowing for real-time feedback and increased accuracy.
Conclusion
Underwater welding plays a crucial role in maintaining and building marine infrastructure, from oil rigs to submerged pipelines. While the job offers unique challenges like water pressure, corrosion, and poor visibility, it also provides an exciting and rewarding career for those willing to tackle the complexities of working in such an extreme environment. With the right techniques, equipment, and safety measures in place, underwater welders can perform tasks that are essential to the world’s growing marine industries.
As technology continues to advance, the future of underwater welding promises even greater innovations, improving efficiency, safety, and precision in this vital field.